Imagine gliding across a calm lake, the water gently touching the hull as you paddle. Building a cedar strip canoe at home is surprisingly easy, even for beginners. But, where do you start? What tools and steps do you need to turn lumber into a beautiful canoe?
Key Takeaways – How To a Build Canoe
- Building a cedar strip canoe at home is a rewarding DIY project for woodworkers of all skill levels.
- The process involves constructing a wooden hull by gluing narrow cedar strips together, then covering the interior and exterior with fiberglass.
- With patience, persistence, and the right tools and materials, anyone can create a durable and functional cedar strip canoe.
- Detailed plans, step-by-step guidance, and a well-equipped workspace are essential for a successful homemade canoe build.
- The final product is a beautiful and customizable wooden watercraft that can be enjoyed for years to come.
Building a Cedar Strip Canoe: An Overview
A cedar strip canoe is a unique watercraft loved by outdoor and DIY fans. Made from thin cedar strips, these canoes are beautiful and offer many benefits. They are perfect for those who want a personal and rewarding boating experience.
What is a Cedar Strip Canoe?
A cedar strip canoe is built by gluing thin cedar wood strips together. This method creates a customizable and lightweight hull. The canoe is then covered in fiberglass for added strength and durability.
Benefits of Building Your Own Canoe
- Customizable design: Building your own canoe lets you design it to fit your needs and preferences.
- Sense of accomplishment: Making your own canoe is rewarding, allowing you to take pride in your creation.
- Cost savings: Building your own canoe can save money compared to buying one, making it a budget-friendly hobby.
- Lightweight and durable: The building process results in a canoe that is both light and strong, ideal for various water activities.
Building a cedar strip canoe is rewarding, whether you’re experienced or a beginner. With the right tools, materials, and guidance, you can make a unique watercraft that will last for years.
Preparing the Workspace and Gathering Materials
Before starting your canoe building project, it’s important to prepare a good workspace. A garage or large workshop with enough space is best. It should be 12-16 feet wide to fit the long cedar wood strips.
This space is crucial for cutting, assembling, and working on the canoe.
Essential Tools and Supplies
To build a cedar strip canoe, you’ll need various tools. This includes a table saw, router, belt sander, and clamps. You’ll also need staple guns and other important items.
These tools are key for shaping, joining, and finishing your canoe.
- Table saw
- Router
- Belt sander
- Clamps
- Staple guns
- Hand tools (hammers, chisels, files, etc.)
Choosing the Right Wood
The main material for a cedar strip canoe is high-quality cedar wood. Look for clear, knot-free boards without defects. The wood’s quality affects your canoe’s look and strength.
You’ll also need plywood, epoxy, and fiberglass cloth for the project.
Having a well-prepared workspace and the right materials is key. It will help you succeed in building your cedar strip canoe.
Constructing the Strongback and Molds
Building a cedar strip canoe starts with a key foundation – the Canoe Strongback and the Canoe Building Molds. These parts are crucial for shaping the Canoe Hull and keeping it strong.
The Canoe Strongback is a long, thin table that acts as a solid base for the canoe’s shape. It’s built with high-quality materials like plywood or strong lumber. This ensures it’s level and stable.
Along the Canoe Strongback, the Canoe Building Molds are placed at regular intervals. These molds are cut with precision using detailed plans or templates. They guide the canoe’s Canoe Hull shape and size.
Building the Canoe Strongback and Canoe Building Molds carefully sets the stage for the canoe’s hull. This focus on detail makes sure the canoe looks great and works well.

Learning to build the Canoe Strongback and Canoe Building Molds is the first step for canoe builders. It lets them start making a unique and personal watercraft.
Milling and Preparing the Cedar Strips
Making a cedar strip canoe starts with careful preparation of the cedar strips. This step, called Canoe Building Wood Preparation, is key to a good build.
First, get the cedar strips. You can order them pre-milled or cut them yourself on a table saw. They should be 3/4 inch wide and 1/4 inch thick. Then, use a planer to Cutting Cedar Strips to exactly 1/4 inch thick.
- Order pre-milled cedar strips or cut your own on a table saw.
- Plane the strips to a consistent 1/4 inch thickness.
- Router a bead-and-cove profile on the edges of the strips.
The last step in Canoe Strip Milling is to add a bead-and-cove edge to the strips. This shape makes the strips fit perfectly around the canoe’s curves. It helps create a strong, lasting hull.
“The attention to detail in preparing the cedar strips is crucial for a successful canoe build. It’s the foundation upon which the rest of the project is built.”
Now that the cedar strips are prepared, the canoe-building journey moves on. The next step is building the strongback and molds. These will shape the canoe’s hull.
Bending and Attaching the Stems
Building the canoe’s stems is key. They are made from three layers of ash wood. The wood is bent and glued to shape them.
This Canoe Stem Bending needs skill and patience. But it makes a strong frame for the cedar strips.
To start Canoe Stem Construction, the ash strips are soaked in hot water. This makes them soft and easy to bend. They are then dried to keep their shape.
After drying, the inner and outer stems are glued together. This creates a strong, three-layer structure.
The last step is Attaching Canoe Stems to the hull. The stems are fastened to the canoe’s ends. This gives a solid base for the cedar strips.
This step needs precise measurements and careful alignment. It’s important to attach the stems correctly for a good canoe design.
Step | Description |
---|---|
1. Soak Ash Strips | Submerge the ash strips in hot water overnight to soften the wood. |
2. Bend Stems | Bend the ash strips around a stem mold and allow to dry for a few days. |
3. Glue Stems | Glue the inner and outer stems together, creating a three-layer structure. |
4. Attach Stems | Securely fasten the inner and outer stems to the ends of the canoe hull. |
Learning Canoe Stem Bending, Canoe Stem Construction, and Attaching Canoe Stems is crucial. It ensures a strong foundation for your cedar strip canoe. This step is vital for a successful project.
How To a Build Canoe at Home: Assembling the Hull
Building the canoe hull is a key part of making a canoe. It starts with stapling the first cedar strip to the molds at the waterline. The cove side faces up. Then, more strips are glued and stapled, overlapping each other as you move up.
Stapling the Strips to the Molds
The Stapling Canoe Strips to molds can be challenging, especially with the curves. But, placing staples carefully keeps the strips in place. This helps you get the right shape. It’s important to be precise and patient for a strong and smooth hull.
Closing the Canoe Hull
When almost done with the Assembling Canoe Hull, you fit and glue the last strips. This step, called Closing the Canoe Hull, needs a lot of attention. It ensures a tight and even fit. With each strip in place, your canoe will come together as a solid and beautiful vessel.
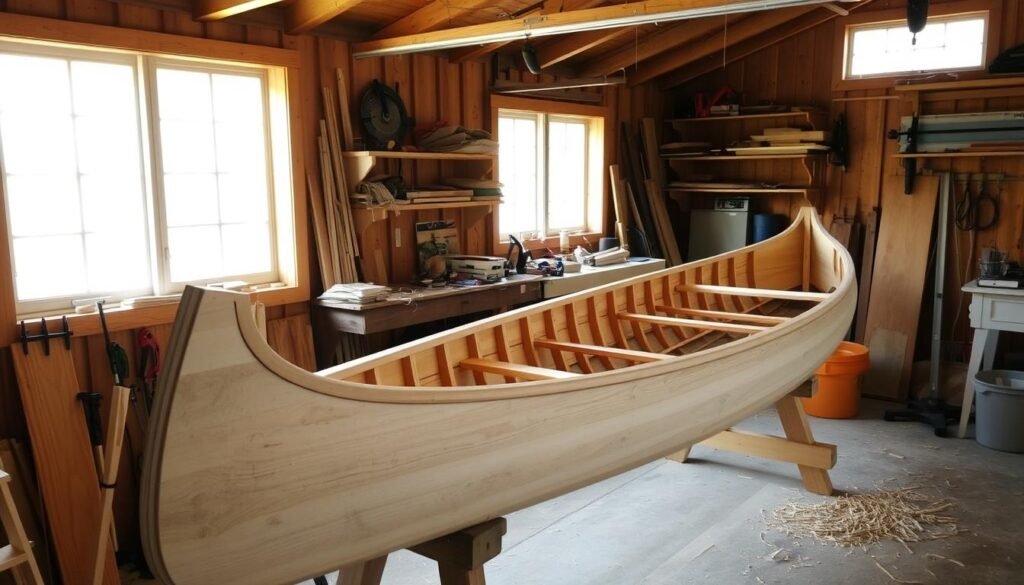
“The true joy of building a canoe lies in the journey, not just the destination. Each step, from selecting the wood to perfecting the hull, is a testament to your dedication and craftsmanship.”
Fiberglassing the Interior and Exterior
After building the cedar strip canoe’s hull, the next step is to apply a protective fiberglass coating. This Fiberglassing Canoe process makes the canoe strong, durable, and waterproof. It prepares the canoe for the challenges of the open water.
The Epoxy Resin for Canoe application involves draping fiberglass cloth over the hull. Then, it’s saturated with high-quality epoxy resin. This method creates a strong barrier that boosts the canoe’s strength and life span.
- Carefully measure and cut the fiberglass cloth to fit the hull’s contours.
- Apply a generous amount of epoxy resin to the surface, ensuring complete saturation of the fiberglass.
- Use a roller or brush to smooth out any air bubbles or uneven areas.
- Allow the resin to fully cure, then sand the surface to achieve a smooth finish.
- Repeat this process, applying multiple coats of fiberglass and resin, to create a durable and protective Canoe Finishing Process.
The careful application of fiberglass and epoxy resin is crucial in the Fiberglassing Canoe process. This layer not only makes the canoe look great but also ensures it lasts long and performs well on the water.
Key Benefits of Fiberglassing the Canoe | Considerations for Optimal Results |
---|---|
Increased strength and rigidity Improved water resistance and waterproofing Enhanced protection against wear and tear Smoother, more uniform surface finish | Proper surface preparation for strong adhesion Careful application to avoid air bubbles or uneven coverage Allowing sufficient curing time between coats Sanding and polishing for a professional-grade finish |
By carefully Fiberglassing Canoe surfaces, you’ll make a stunning and durable cedar strip canoe. This important Canoe Finishing Process using Epoxy Resin for Canoe ensures your homemade craft will last for years. It will give you years of enjoyment on the water.
Adding Finishing Touches
As your cedar strip canoe nears completion, it’s time for the final touches. These will make it both beautiful and functional. The Canoe Gunnels, Decks, Seats, and Yoke are essential. They turn your canoe into a masterpiece.
Gunnels and Decks
The Canoe Gunnels are wooden rails that strengthen the canoe and add beauty. They are attached with epoxy and screws for a strong bond. Small Canoe Decks at the ends add to the look and provide storage.
Seats and Yoke
The Canoe Seats and Yoke improve the canoe’s use and show off your skill. The seats are made with epoxy for water protection. The cane weaving is done by hand, adding traditional charm. The Yoke makes carrying the canoe easy and balanced.
These finishing touches are more than looks. They make the canoe sturdy, beautiful, and functional. They ensure hours of fun on the water.
Conclusion – How To a Build Canoe
Building a cedar strip canoe at home is a rewarding project, even for beginners. It requires patience, persistence, and the right tools and materials. By following a detailed process, you can create a beautiful and functional canoe.
The joy of finishing a Completed Canoe is unmatched. There are many online resources and communities to help you. Whether you’re experienced or new to DIY, you’ll find the journey rewarding. You’ll gain a cherished vessel and appreciate the art of canoe making.
If you’re thinking about building your own cedar strip canoe, start now. The memories and sense of achievement are worth it. You’ll have a unique craft to call your own, ready for your adventures on the water.
FAQ – How To a Build Canoe
What is a cedar strip canoe?
A cedar strip canoe is made by gluing narrow wooden strips together. Then, it’s covered with fiberglass inside and out. This method is easy and great for beginners.
What are the benefits of building your own canoe?
Building your own canoe lets you customize it. You’ll feel proud of your creation and save money. Plus, cedar strip canoes are light, strong, and perfect for fun trips.
What tools and materials are needed to build a cedar strip canoe?
You’ll need a table saw, router, and belt sander. Clamps, staple guns, and hand tools are also key. High-quality cedar, plywood, epoxy, and fiberglass cloth are the main materials. Choosing clear cedar is important for a smooth hull.
How do you construct the strongback and molds for a cedar strip canoe?
The strongback is a long table for the canoe’s shape. Plywood molds are mounted along it to guide the hull’s curve. These molds are cut from plans and are vital for the canoe’s shape.
What is the process of assembling the cedar strip canoe hull?
Start by stapling the first strip to the molds at the waterline. Then, add more strips in an overlapping pattern, working up. The curves can be tough, but staples keep the strips in place. Finally, join the sides with the last strips.
How do you apply fiberglass to the canoe?
Drape fiberglass cloth over the hull and soak it with epoxy. This creates a strong, waterproof layer. Apply multiple coats, sanding between each to smooth the finish. This makes the canoe strong and durable.
What are the final touches added to a cedar strip canoe?
Add gunnels, decks, seats, and a yoke last. Gunnels are attached with epoxy and screws. Decks, seats, and yoke are coated with epoxy for water resistance. The cane weaving on seats is done by hand.